A habblokkok telepítésének és gyártásának kiválasztása otthon
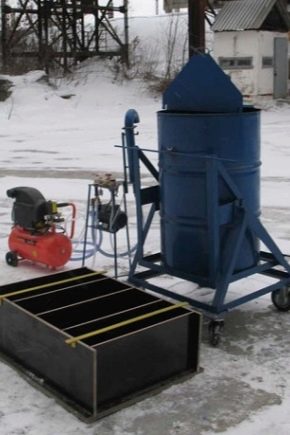
A habbeton nagyon népszerű anyag az alacsony épületekben. Az ipari gyártás mellett önállóan is készül. A különböző típusú blokkok kiadása nyereséges üzlet lehet. A habblokkok otthoni gyártása azonban számos tulajdonsággal rendelkezik. A szükséges egység megvásárlása előtt ismernie kell magának az anyagnak a jellemzőit, a megfelelő eszközök kiválasztását, valamint a felhasznált keverékek fogyasztását.
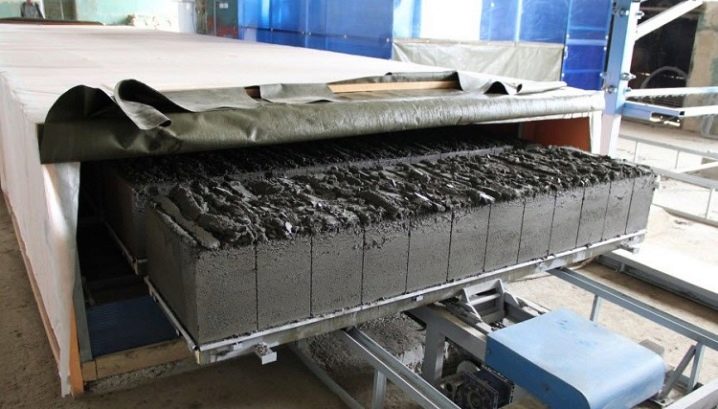
Anyagi jellemzők
A habblokkok habarcsból készülnek, amely a következőket tartalmazza:
- homok;
- portlandcement;
- habképző szer (habkoncentrátum);
- víz.
Ebben az esetben a habbeton térfogatsűrűsége eltérő lehet. Valójában sejtes szerkezetű beton. Zárt légbuborékok tömege alkotja. Ez a tulajdonság határozza meg az anyag alacsony sűrűségét, valamint hővezető képességét. Különböző sűrűségű habblokkok hőszigetelő, szerkezeti-hőszigetelő és alacsony hővezető képességű szerkezeti anyagokként használhatók.
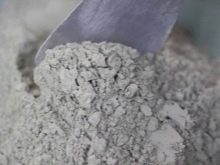
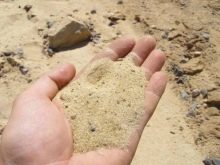
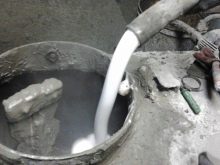
Általában a habbeton márkája határozza meg a sűrűségének szintjét. Minél alacsonyabb, annál kevesebb keveréket használtak az anyag előállításához. Ez a tény az önköltségi árban is megmutatkozik (a habbeton olcsóbb, mint a beton). Viszonylag alacsony sűrűsége miatt azonban előnyös anyagnak tekinthető a házon belüli válaszfalak építéséhez.
A habblokk könnyen feldolgozható, tipikus fémfűrésszel vágható. Ráadásul nem esik össze, ha szöget vernek bele. Munkájában fára hasonlít, alakjában téglalap. A blokkok különböző méretűek lehetnek: a szabványos elemektől a nagyon nagyokig.
A házi készítésű habbeton méretei a megvásárolt egység alakja alapján határozhatók meg.
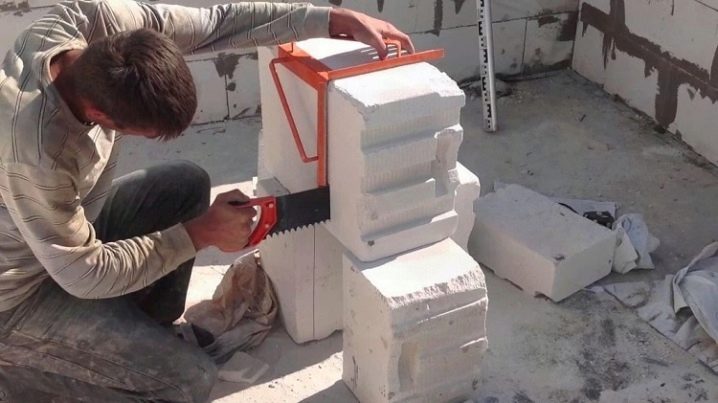
Előnyök és hátrányok
A habbeton számos előnnyel rendelkezik, amelyeknek köszönhetően az építőiparban igény van rá. Ez az anyag gyakorlatilag nem változtatja meg minőségét és teljesítményét az idő múlásával, nincs kitéve az öregedésnek. A környezetbarátság ártalmatlanná teszi a gyártó, az építők és a háztartások egészségére. Nem bocsát ki mérgező anyagokat a levegőbe, tartósnak és megbízhatónak számít, jó hőszigetelést garantál.
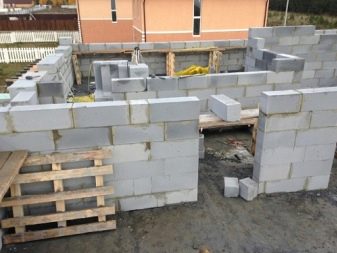
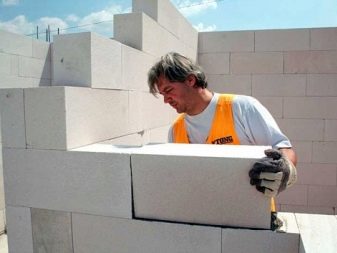
Ezenkívül magas hangszigetelő tulajdonságokkal rendelkezik, lehetővé teszi a zajszint csökkentését, ami fontos a modern ember számára. A habblokk tűzálló. Képes stabilizálni a beltéri hőmérsékleti hátteret, könnyen beépíthető, emellett magas a termelési jövedelmezősége is. Kis súlyának köszönhetően nem hoz létre olyan kolosszális terhelést, mint a beton. Ez lehetővé teszi a költségek csökkentését az alapítvány telepítésekor.
Az előnyök mellett azonban a habbetonnak hátrányai is vannak. Például annak ellenére, hogy tartósnak tekinthető, veszít a betonnal és a vasbetonnal szemben. Egyéb árnyalatok közé tartozik az a tény, hogy a habblokk nem működik hajlításkor. A nedvességgel szemben is instabil, mivel képes felszívni a környezetből.
Függetlenül attól, hogy az anyagot termelésben vagy otthon állítják elő, zsugorodni fog.
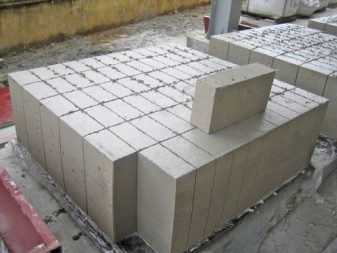
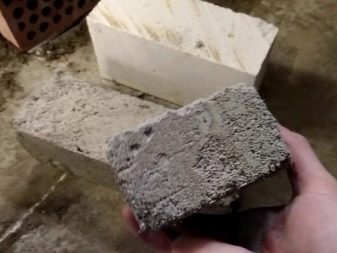
Berendezések és eszközök
Habblokkok otthoni készítésekor a következő felszerelésekre és tartozékokra lehet szüksége:
- adagoló cementhez és homokhoz;
- legalább 200 l / perc kapacitású habgenerátor;
- baro installáció;
- használt vízadagoló;
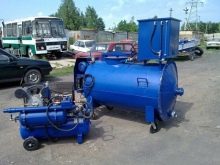
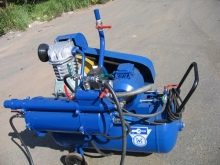
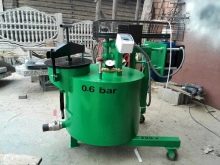
- vibrációs szita (alapanyag szita);
- kész keverék kivezető tömlő;
- kompresszor;
- legalább 250 liter térfogatú betonkeverő;
- speciális formák tömbökhöz vagy vágógéphez.
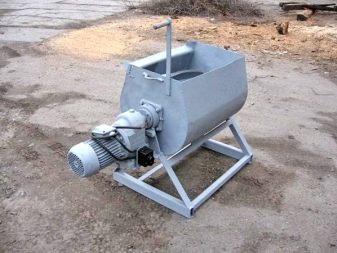
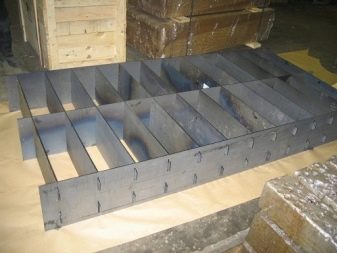
Nem lesz nehéz ma otthon megvásárolni az építőanyagok gyártásához szükséges berendezéseket. Kívánság szerint nemcsak egy teljes gyártósort vásárolhat, hanem annak egyes alkatrészeit is. Érdemes megfontolni, hogy a habblokkok otthoni gyártására szolgáló berendezések nemcsak helyhez kötöttek, hanem hordozhatók is. A vonal lehet szállítószalag vagy automata. Ezek a tényezők határozzák meg a vásárolt berendezés költségét.
Minden berendezés középpontjában a habgenerátor áll. Egy ilyen eszköz naponta körülbelül 100-110 köbméter anyag kibocsátását tudja biztosítani. Az álló vonalak megkülönböztető jellemzője a magas termelékenység, valamint a kiváló minőség és az alacsony költség. Figyelembe véve, hogy egy ilyen készlet körülbelül 1,5 millió rubelbe kerül, ez megkérdőjelezi a vásárlást.
A mobil habbeton üzemhez nem szükséges drága habgenerátor vásárlása, ami keresletté teszi az építőipari piacon. Ezzel együtt azonban nem büszkélkedhet nagy teljesítménnyel. Általában ebben az esetben nyomásbeállítást alkalmaznak, de teljes erejével nem képes napi 40-45 köbméternél több készanyagot előállítani.
Ebben az esetben gyakran kész blokkokat készítenek nagy habosítószer-felhasználással.
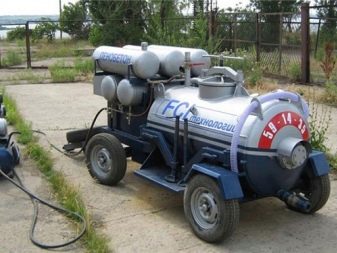
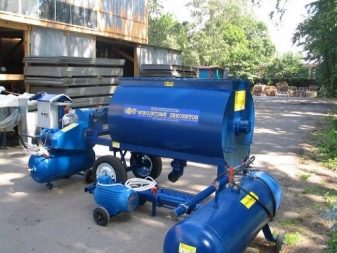
Erősségük gyengébb, mint az álló vonalakon létrehozott analógok. Az otthoni termelés teljes készletének ára 50 és 300 ezer rubel között változhat. Ugyanakkor a nagy teljesítményű berendezések általában magas költségekkel járnak. Például egy 300 000 rubel készlet körülbelül 72 köbméter habbetont adhat naponta.
Az automata vonalhoz nagy területekre van szükség, ami gyakran problémás, mert eredetileg nem biztosították. Az ilyen vonalakhoz általában szükség van a cement, a víz, a homok, valamint az automatikus adagolású adalékanyagok tárolására. Ezenkívül át kell gondolni a habbeton szárításának, formákba öntésének, valamint a vágáshoz való beszerelésnek a területeit. Ez a berendezés naponta átlagosan körülbelül 80-100 köbméter anyagot képes előállítani, de nem mindenki engedheti meg magának ezt a luxust, mert a készlet 1,5-3 millió rubelbe kerül.
Amikor a kezdeti szakaszban nincs elég pénz, használt felszerelést vásárolnak. Ebben az esetben azonban fel kell készülni arra, hogy egyes alkatrészeket elég gyorsan kell cserélni.
Ezenkívül meg kell értenie, hogy a működő berendezés a kész habbeton rossz minőségét okozhatja.
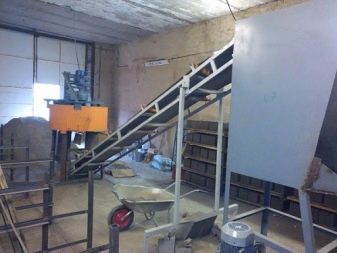
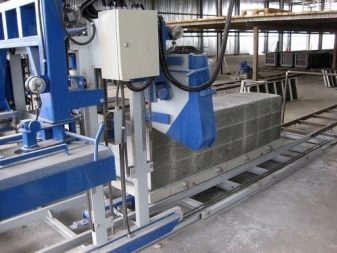
A habbetonhoz vásárolt formák eltérőek lehetnek. Ma acélból, rétegelt lemezből és műanyagból készülnek. A termékek kapacitása eltérő, például vásárolhat 390x190x288 mm-es műanyag formákat, 588x300x188 mm-es rétegelt lemezeket, 600x300x200 mm-es acél megfelelőket. Vásárlásukkor fontos figyelembe venni a geometria szigorúságát, mivel a kész anyag minősége közvetlenül ettől függ. A szimmetria legkisebb megsértése is elfogadhatatlan.
A habbeton tömeg öntésére szolgáló formák kiválasztásakor ügyelni kell a gyártás anyagára. Tekintettel arra, hogy a zsaluzat kombinálható, ez különösen fontos. Például, ha az eladó megjegyzi, hogy a nagy teherbírású műanyag betétekkel ellátott fém változat még a legmagasabb hőmérsékletet is bírja, akkor ebben nem szabad vakon bízni.
Az a tény, hogy az ilyen formák valójában rövid életűek. A habbeton tömeg száradása és keményedése során nagy mennyiségű hő szabadul fel.
A műanyag, bármilyen jó minőségű is, reagál a hőmérséklet emelkedésére.
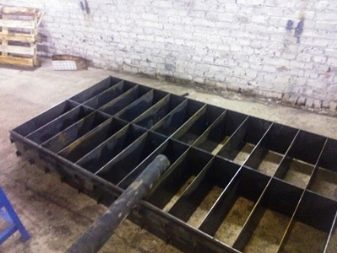
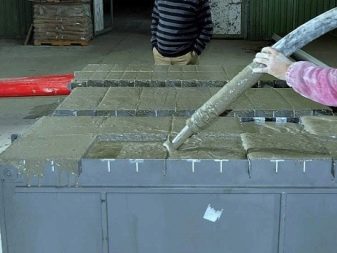
A keverék fogyasztása és arányai
A habbeton gyártásánál az összetevők aránya a következő: 320 kg cementhez (például M500 márka) 420 kg homokot, 45 liter vizet a hab előállításához és 120 liter vizet az oldathoz. . Ami a habosítószert illeti, annak fogyasztása egy adott márkától függ. Általában ilyen térfogathoz 1,2-1,5 kg tartományban használják. A termeléshez szükséges víz nemcsak csapvízből vehető, hanem közepes keménységű műszaki víz is megfelelő.
A recept és az arányok közvetlenül függenek a habbeton sűrűségétől, amelyet végül meg kell szerezni. Például, ha szüksége van a D 600 habtömbök térfogatsűrűségére, vegyen 210 kg homokot, 310 kg cementet, 110 liter vizet a habarcshoz és 54 litert a hab hígításához. Ezen kívül 1,3 kg habkoncentrátum és 715 liter hab az építőelem. A komponensek teljes mennyiségének összekeverésekor 685 kg nedves tömeget kapunk.
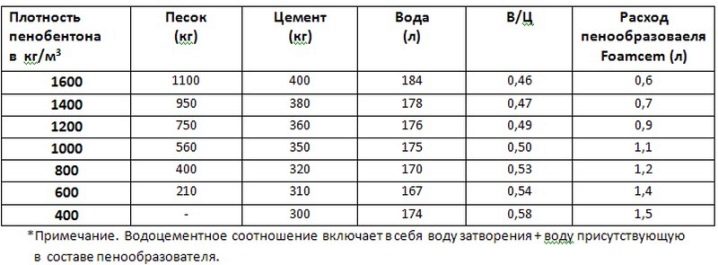
Ha nagy sűrűségre van szükség (például 1000 kg/m3), a pórusbeton masszát 590 kg homokból, 350 kg cementből, 120 liter oldatban lévő vízből, 42 liter habból készítik. Egy ilyen recepthez legfeljebb 1 kg habkoncentrátumot és 560 liter habot használnak. Ennek eredményeként az utóbbi esetben a habblokkok előállításához szükséges nyersanyagok tömege 1103 kg lesz.
Fontos figyelemmel kísérni a kapott hab és oldat homogenitását. Ez növeli a kész anyag minőségi jellemzőit. A kívánt recept kiválasztásakor szem előtt kell tartani, hogy a jelenlegi GOST szerint a kész anyag zsugorodása nem haladhatja meg a 3 mm-t 1 négyzetméterenként. m.
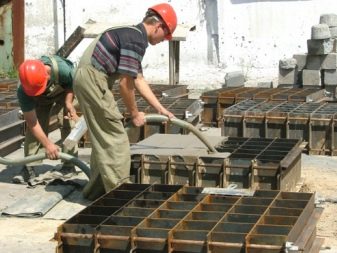
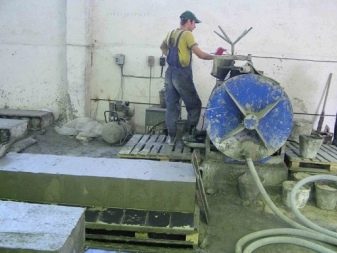
Hogyan kell csinálni?
A habblokkok otthoni gyártása kétféleképpen történik: öntés és fűrészelés. A klasszikus barkácsgyártási technológia speciális kazettás formák használatát foglalja magában, kivehető válaszfalakkal és oldalakkal, hogy a teljes kapacitást azonos méretű különálló részekre osztják fel. Az ilyen formákban az oldat megszárad és megkeményedik, majd a kész habbetont eltávolítják. Az építőanyag-gyártás ezen módszerének fő előnye az a tény, hogy a monolit blokkot nem kell vágni.
Így nincs szükség fűrészgép vásárlására, ami csökkenti a felszerelés költségeit. Azonban a forma az, ami a szigorú geometria megsértését okozhatja. A keményedés után nem minden a formába öntött elem lesz tökéletesen egyenletes, még drága szerelvény vásárlása esetén sem. Házasság mindenképpen lesz, ez pedig plusz költség a felhasznált keverékhez.
A habtömbök tönkremenetelének megelőzése érdekében speciális kenőanyagot kell használni, amely a szabadban néhány napon belül lebomlik.
Az ilyen anyagok nem olcsók, de ha nem használják őket, ez a habtömbök forgácsát vagy repedését okozhatja.
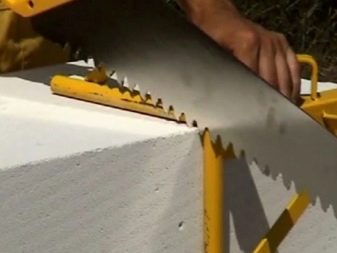
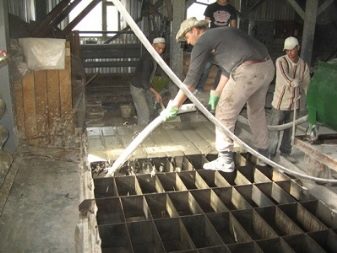
Leggyakrabban a fűrészelési technológiát használják az otthoni termelésben. Ebben az esetben először egy nagy formát öntünk ki, amelyet ezt követően adott méretű különálló elemekre vágunk. Ehhez a módszerhez fűrészgépet vásárolnak. Bár némi pénzügyi befektetést igényel, a jövedelmezőség növekedni fog. Ennek a módszernek az előnyei az egyes elemek szigorú geometriája, valamint a forgácsképződés minimalizálása a habblokkok szélein.
Ez a technika azonban jól megütheti a pénztárcát, mivel kisméretű munkadarabok előállításához speciális berendezések szükségesek, és ez drága. Ezenkívül a monolit födém apró darabokra vágása megnöveli az anyag előállításához szükséges időt.
A vágógép kétféle változatban kapható. Az első esetben ez egy olyan egység, amelyen a monolit anyagot azonnal vágják, miután megszilárdult (deformálódott). Ez azért kényelmes, mert nem kell a teljes táblát átvinnie a fűrészgépbe, ezáltal csökkentve a munkaerőköltségeket és az időt. A habblokkokat speciális zsinórokkal vágják, amelyeket nagy vágási pontosság jellemez.
Ezeknek a vágóelemeknek a hátrányai a törékenységük, valamint a tisztességes költségük.
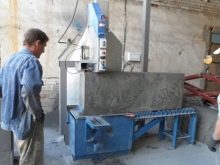
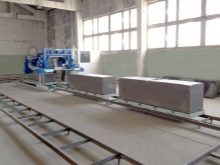
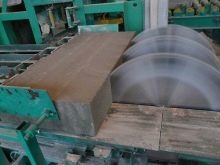
A második típusú vágóberendezéshez habbeton monolit átvitele szükséges a vágáshoz. Ebben az esetben tárcsás késekkel kell vágni. A húrokkal ellentétben az ilyen kések tartósak, és maguk az egységek karbantartása gazdaságos. A habbeton födémek áthelyezése azonban enyhén szólva kényelmetlen és problémás.
A habtömbök keményítése kétféleképpen történhet: természetes és autoklávban. Ugyanakkor a második módszerrel szárított elemek rendelkeznek a legjobb minőségi jellemzőkkel. Így lehetőség nyílik a legkedvezőbb feltételek megteremtésére a jó építőanyag megszerzéséhez. Az ilyen berendezések ára azonban jelentősen megüti a zsebet, ezért ha kis mennyiségben gyártják, nem vásárolják meg.
Az önszáradó habbeton jobban szárad nyáron. Általános szabály, hogy ha a helyiség hőmérséklete a szárítás során nulla alatt van, le kell fedni a zsaluzatot, vagy át kell gondolni a habblokkok gőzölésére szolgáló speciális kamrák létrehozását. Az első esetben általában polietilént vagy ipari vattát használnak. A másodikban a gyártóműhely belsejében egy helyiséget osztanak ki ezekre az igényekre.
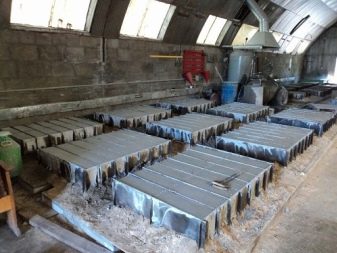
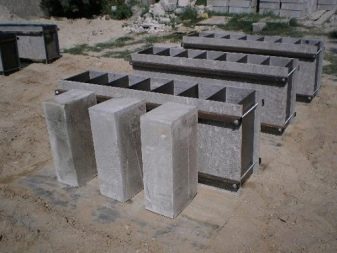
Egy ilyen helyiségben speciális hőmérsékleti rendszert hoznak létre, figyelembe véve a szükséges páratartalmat a blokkok egyenletes és helyes keményítéséhez. Gyakran gőzfejlesztőket használnak erre a célra, így próbálják automatizálni a munkafolyamatot. Ha nincs többletpénz, de nem akarja növelni a habblokkok száradási idejét, különböző költségvetési lehetőségeket alkalmaznak a probléma megoldására. Valaki vödör vizet helyez a kamrába, egy másik esetben a gázfűtéssel történő kommunikációt végzik el.
Azok, akik nem elégedettek ezekkel a megoldásokkal, a gyártócsarnok egy részét bezárják bármilyen rendelkezésre álló anyaggal, amely elfogadható áron nevezhető. Kerítésként például régi téglákat, profillemezeket vagy akár ugyanazokat a habblokkokat használnak. A kamra gázzal történő gőzölésekor figyelembe kell venni a kiválasztott üzemmód optimálisságát. Ideális esetben a helyiség páratartalma nem lehet kevesebb, mint 65%. Ha azonban a gyártás nem rendelkezik speciális berendezések beszerzéséről hő- és párakamra formájában, ez befolyásolhatja a kész anyag tanúsítását.
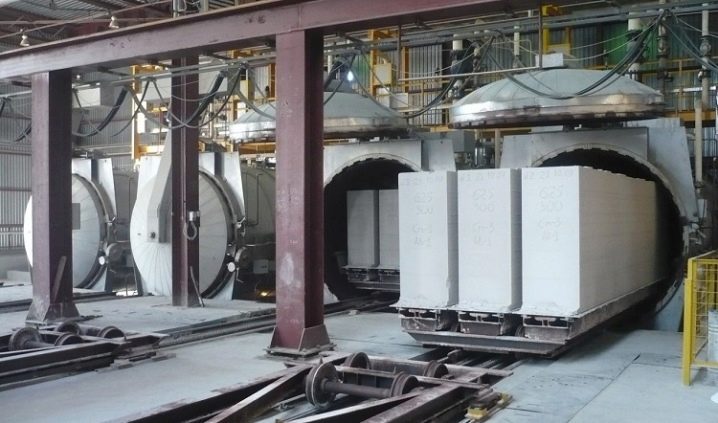
Gyártási technológia
A habbeton blokkok otthoni készítésének szabványos technológiája több műveletből áll.
- Kezdetben habkoncentrátumot készítenek egy külön tartályban. Ezután vízzel kombinálják és gőzfejlesztőbe küldik. Ha a független gyártás rendelkezésére áll egy kavitációs egység, amely ultrahang segítségével felhabosítja a tartalmat, akkor ez a szakasz kimarad.
- A következő lépés a habbeton keverék elkészítése. Ehhez a keverék szükséges összetevőit és a speciális adalékokat a keverőkamrába helyezik. Ezt követően a kamrát megtöltjük az előzőleg elkészített habbal. A technológiai szabályok szerint a keverés a kamrában néhány percen belül megtörténik.
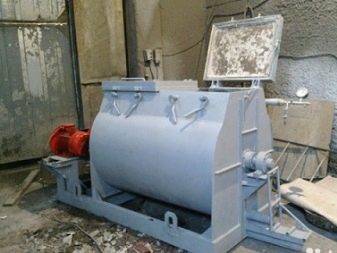
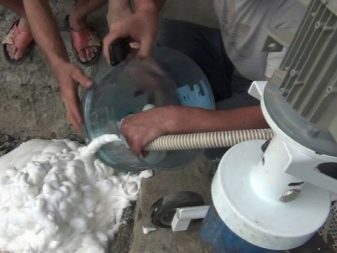
- Ha a gyártás során kavitációs egységet használnak, kezdetben habosítószert helyeznek a kamrába a keveréshez... Ebben az esetben a munkaoldat többi komponensét később helyezzük el. Ebben az esetben a keverési idő nem haladhatja meg a 0,5 percet. Ebben a szakaszban az oldat készen áll az öntésre.
- Keverés után a készítményt a meglévő formákba öntjük. Annak érdekében, hogy a massza ne tapadjon a berendezés felületére, az érintkezési helyeket előkenjük gépolajjal vagy speciális kenőfolyadékkal. Kívánatos, hogy a helyiség hőmérséklete a készítmény megszilárdulása és keményedése során legalább +20 ° C legyen. Körülbelül 8-10 óra elteltével a habbeton szilárdságának negyedét nyeri el.
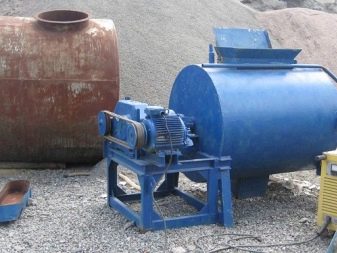
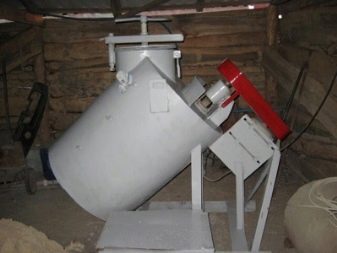
Ez a legalkalmasabb idő a vágáshoz, figyelembe véve a szükséges méreteket, valamint a csomagolást. Az elemek a gyártástól számított 28 nap elteltével nyerik el a végső szilárdságot. Az edzési szilárdság az adott harmadának számít.
A termék két napon belül értékesíthető.
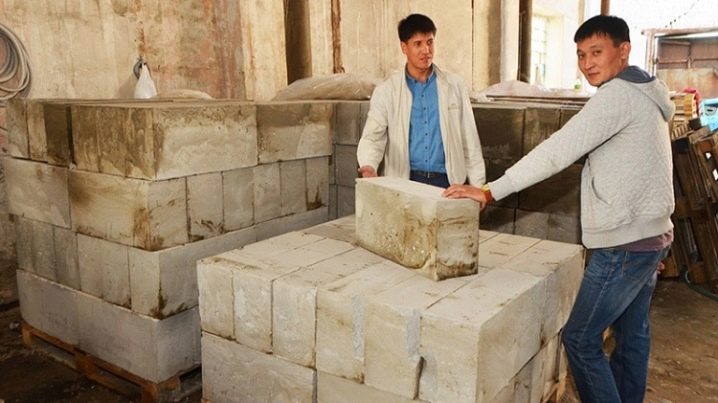
Mit kell figyelembe venni?
Néha úgy tűnhet, hogy sokkal könnyebb önállóan gyártani a habblokkok gyártására szolgáló berendezéseket, alapvető ismeretek, teljesítményszámítás és rajzok felhasználásával, amelyeket ma nem lesz nehéz megtalálni az interneten. Valójában azonban érdemes megfontolni: a habbeton gyártása egy otthoni miniüzemben nem teszi lehetővé a pontatlanságokat, mivel előnyei ettől függenek. Meg kell értenie, hogy szélsőséges esetekben a gyári terméket nem lesz nehéz a jövőben szükségtelenként eladni, míg a házi készítésű termékek igény nélkül maradnak.
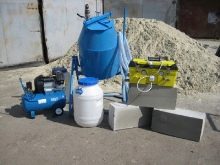
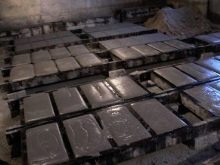
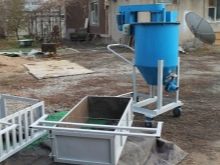
A habblokkok gyártásához M 500 márkájú portlandcementet használnak. A kész elemek minőségi jellemzőinek javítása érdekében különféle adalékanyagokat adnak hozzá. Például a "Bio NM" módosító használatával javíthatja a habtömbök fagyállóságát. A "Bio-Lux" és a Laston adalékoknak köszönhetően növelhető a levegő koncentrációja az anyag szerkezetében.
Ahhoz, hogy a kész anyag kiváló hőszigetelő tulajdonságokkal rendelkezzen, gyártásához ipari típusú habképzőt kell vásárolni. Bármennyire is szeretne pénzt megtakarítani és saját kezűleg elkészíteni, nem lesz olyan hővisszatartási aránya, mint a gyártás során készített opciónak.
Az is fontos, hogy a jó minőségű habblokk alapját a jó minőségű alapanyagok képezzék.
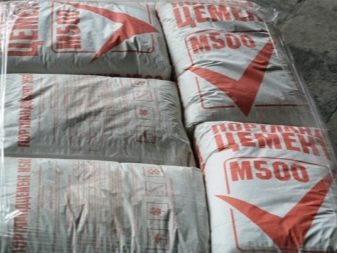
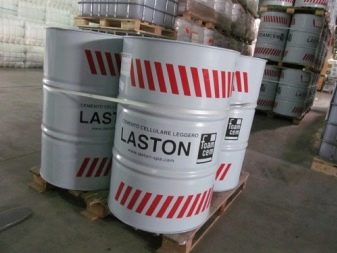
Az alábbi videó megtekintésével megtudhatja az otthoni habblokkok készítéséhez szükséges utasításokat.
A megjegyzés sikeresen elküldve.